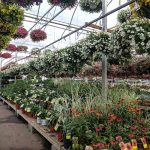
10 Amazing Advantages Of Dutch Trolleys
January 24, 2024
Top 3 methods to prevent corrosion
February 22, 2024Efficient pallet racking systems are crucial to streamlining storage operations and increasing the capacity of a warehouse. This blog post sheds light on the do’s and don’ts of pallet racking systems to ensure maximum safety and efficiency of your warehouse.
The Benefits of Installing Pallet Racking Systems
Pallet racking systems offer a multitude of benefits for warehouses, revolutionizing storage and optimizing space utilization. Firstly, they enhance efficiency by enabling easy access and organization of inventory, streamlining picking, packing, and storage processes. Their modular design allows for flexibility in accommodating various pallet sizes and configurations, maximizing storage capacity while minimizing wasted space. Additionally, these systems enhance safety by reducing the risk of accidents associated with manual handling, ensuring proper load distribution and stability. Moreover, they contribute to cost-effectiveness by improving inventory management, reducing product damage, and ultimately enhancing overall warehouse productivity and workflow efficiency.
Now that we have covered the importance of pallet racking systems, let’s focus on some of the do’s and don’ts of pallet racking.
Do’s and Don’ts of Pallet Racking
Key Dos of Pallet Racking Systems
1. Prioritize Safe Pallet Rack Storage Practices
Regular inspections should include checking for rust, dents, or misalignments and promptly addressing any issues to maintain rack integrity. Additionally, incorporate safety mechanisms like pallet stops or anti-collapse mesh to prevent accidental dislodging or falling of items, enhancing overall safety measures within the warehouse.
2. Implement Warehouse Safety Best Practices
Encourage a culture of reporting and addressing safety concerns promptly among employees, fostering a proactive approach to maintaining a safe working environment. Furthermore, regularly review and update safety protocols in line with evolving best practices and industry standards to ensure ongoing staff awareness and compliance.
3. Pay attention to Loading and Unloading Procedures
Implement a rotation system for inventory to prevent overloading specific rack sections and ensure even distribution of weight across the warehouse. Conduct thorough assessments before implementing any changes in inventory or storage configurations to ensure racks can accommodate alterations without compromising safety. Furthermore, maintain detailed records of load capacities and adjustments made to prevent confusion or oversight regarding rack capabilities.
4. Conduct Employee Training Sessions
Conduct regular training for employees responsible for loading and organizing to ensure consistent adherence to safety guidelines. Provide regular refresher courses or toolbox talks to reinforce safety practices and keep them at the forefront of employees’ minds. Additionally, create designated areas for specialized equipment and ensure their accessibility and proper usage to maintain a safe work environment. All employees must have adequate knowledge of proper handling and lifting techniques, reducing the risk of workplace injuries due to improper practices.
5. Take Notice of Weight Limits and Load Capacity
Conduct periodic load testing and stress analysis to confirm racks’ structural integrity and validate their load-bearing capacity, ensuring they consistently meet safety standards. Additionally, establish clear procedures for reporting any signs of overloading or strain on racks to swiftly address potential risks.
6. Choose the Right Components
Collaborate with engineers or rack system experts to help you in choosing the right pallet rack components to optimize space and ensure maximum safety. Consider implementing seismic bracing or additional reinforcements for racks in areas prone to earthquakes or other natural disasters, prioritizing safety in warehouse design.
7. Regularly Review the Safety Measures
Engage in regular reviews and assessments of safety measures and accessories to ensure their effectiveness and relevance in the evolving warehouse environment. Periodically review and update the warehouse’s layout and rack configurations based on changing needs and safety standards to maintain optimal safety levels.
Key Don’ts of Pallet Racking Systems
1. Steer Clear of Overloading
When discussing the do’s and don’ts of pallet racking, overloading is a crucial aspect that cannot be ignored. It can lead to catastrophic consequences such as rack collapse, endangering employees, damaging inventory, and disrupting operations. Exceeding the weight capacity specified by the manufacturer puts excessive stress on the structure, weakening it over time and making it susceptible to failure.
2. Never Ignore Damage
Ignoring even minor damage, such as bent beams, dented uprights, or missing connectors, poses a severe risk to the integrity of the racking system. Small damages can worsen over time, compromising the structural integrity and stability of the entire system. Regular inspections should be conducted, and any identified issues should be addressed promptly through repair or replacement.
3. Avoid Improper Use of Equipment
Using damaged or malfunctioning equipment, such as forklifts, pallet jacks, or handling machinery, within the vicinity of the pallet racking system can cause significant damage. Mishaps due to faulty equipment can lead to collisions with the racks, resulting in bent or dislodged components. This can weaken the structural integrity of the racks and create safety hazards.
4. Eliminate Inconsistent Procedures
Lack of standardized procedures for loading, unloading, or handling pallets can lead to uneven weight distribution or incorrect positioning. Inconsistencies in procedures and a lack of safety accessories for pallet racking can create imbalances in the racks, causing stress on specific areas and compromising stability. This inconsistency may also affect inventory placement and retrieval efficiency.
5. Don’t Neglect Training
Inadequate or inconsistent training of personnel handling the pallet racking system can result in errors during loading, unloading, or inspection processes. Improper handling techniques can lead to accidents, damage to racks, or incorrect assessment of rack conditions, increasing the risk of structural failure.
6. Never Avoid Maintenance
Skipping or delaying regular maintenance routines can lead to undetected issues that worsen over time. Failure to address maintenance needs, such as cleaning, repairing, or replacing damaged components, can result in more significant problems, ultimately compromising the safety and functionality of the racking system.
Final Thoughts
Maintaining pallet racking systems requires strict adherence to safety protocols, regular inspections, and staff training. By avoiding these common pitfalls and adhering to proper protocols, companies can maintain a safer and more efficient pallet racking system, ensuring the protection of both personnel and inventory while optimizing warehouse operations. Prioritizing these measures and following the do’s and don’ts of pallet racking safeguards both personnel and inventory, fostering a secure and efficient warehouse environment.
Also, if you are looking for the best storage solution, then Midwest Distribution can help. With years of experience in the industry, we know exactly what your warehouse needs. So contact us to get the perfect warehousing solution that is sure to boost your productivity.