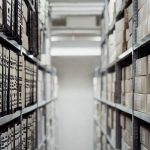
7 signs of warehouse racking collapse
October 13, 2023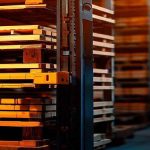
Different Pallet Types And Their Uses: A Guide For Beginners
November 15, 2023Warehouse racking layout is a unique puzzle where every piece represents an aspect of warehousing, and the challenge lies in fitting them all together perfectly. To complete this puzzle efficiently, you must consider some factors that can influence the productivity of your warehouse. Let’s take a look at what those factors are.
Understanding The Basics Of Warehouse Racking Layout
The heart of a bustling warehouse lies in its racking layout—an intricately woven web of structure and organization. Every shelf, every aisle, and every corner serves a purpose, influencing the warehouse’s functionality and productivity. The warehouse racking layout is the backbone of a warehouse’s operational prowess, where every decision shapes the efficiency and agility of material flow. So, while learning about factors that affect this design, we must understand its components and their functions.
Factors To Consider For Warehouse Racking System Design
1. Warehouse Rack Design Components And Their Functions
Frames: They are vertical components that provide structural support to the rack system. They bear the weight of the stored items and transmit it to the floor.
Cross Beams: Beams are horizontal components that connect to the uprights to create levels or shelves for storing goods. They play a critical role in distributing the weight of the items across the uprights.
Deck Panels: These are used to create a stable and safe surface on the beams. They provide support for items that may not sit well on pallets alone and prevent smaller items from falling through the gaps.
Pallet Supports: Pallet supports are placed on the beams to enhance the stability of palletized loads. They ensure the pallets are properly supported and reduce the risk of sagging or damage.
End Frames: End frames protect the uprights from potential damage caused by forklifts or other material handling equipment. They help maintain the structural integrity of the rack system.
Row Spacers: Row spacers maintain the appropriate distance between rows of racks, optimizing aisle width and ensuring safe movement within the warehouse.
Understanding how these components work together and their functions is essential for designing a warehouse racking layout that maximizes storage capacity, accessibility, and safety while minimizing costs and space wastage.
2. Analysis Of Your Inventory
Understanding the nature of the products you handle and their storage requirements is fundamental to designing an efficient pallet racking system design. Consider the size, shape, weight, and fragility of the products. Different products may require specialized storage solutions, such as pallet racks for heavy goods or specialized racks for fragile items.
You must also analyze how frequently products are accessed and moved. High-turnover items might benefit from easily accessible storage like selective pallet racking, while slow-moving items can be stored in higher-density storage systems like drive-in racks. Moreover, If your inventory varies throughout the year, the racking system should allow flexibility and adjustability to accommodate changing storage needs.
3. Storage Requirements For Products
The storage needs of the products directly influence the type of warehouse racking layout. First, determine whether your products are typically stored on pallets, in bins, or as loose items, as this affects the choice of rack type. You must also evaluate the need for high-density storage. This informs decisions about rack height, aisle width, and storage systems like narrow-aisle racking or mezzanine platforms.
4. Need for Special Storage Requirements
Specialized storage solutions are needed to meet the unique requirements and characteristics of certain products. Different products have distinct properties, storage needs, and handling requirements that necessitate tailored storage solutions to ensure their safety, integrity, accessibility, and compliance with regulations.
Many products, such as perishable goods, hazardous materials, delicate items, or high-value items, require special consideration for storage. For perishable goods like fresh produce and pharmaceuticals, cold storage or refrigerated environments are vital to maintain freshness and prevent spoilage.
Fragile items like glassware necessitate protective packaging and specific rack designs to prevent breakage, while heavy or bulky items like machinery parts call for heavy-duty racks capable of supporting substantial weight. High-value items, such as jewelry and valuable electronics, require secure, monitored storage with additional security measures for utmost protection.
When designing a warehouse racking layout, you must consider the type of products available in your inventory so that you can create an adequate storage environment for them.
5. Building’s Pallet Racking layout
Efficient utilization of space within the warehouse is highly dependent on the dimensions and structural elements of the building to optimize storage capacity and accessibility. The height of the warehouse should be utilized effectively by designing racks that capitalize on vertical space.
The pallet racking layout should also consider the placement of columns within the warehouse to ensure they don’t hinder the racking system’s efficiency. Racks should be strategically positioned to work around these structural elements.
6. Space Utilization To Maximize Efficiency
Efficient utilization of warehouse space is a core objective in designing a warehouse pallet racking system. Optimizing space ensures cost-effectiveness and enables seamless operations. Here are some pallet rack ideas that we can consider to optimize space:
Dynamic Slotting: Implement dynamic slotting strategies that place high-demand products in easily accessible areas, optimizing pick paths and reducing retrieval times.
Cubic Space Utilization: Racks should be designed to utilize the entire cubic space of the warehouse, including height, width, and depth, to maximize storage capacity.
Bulk Storage vs. Selective Storage: Depending on inventory characteristics, choose between bulk storage options for high-density storage or selective storage for easy accessibility and picking.
7. Traffic flow In Aisles
A well-planned traffic flow ensures that material-handling equipment and personnel can move easily and safely within the warehouse. It is better to design aisles to accommodate the type of material handling equipment used, ensuring they are wide enough to prevent congestion and allow safe movement.
To further increase productivity, you can evaluate the pros and cons of one-way and two-way aisles in relation to your operations and choose the most efficient layout for your warehouse and business model.
8. Safety Precautions And Considerations
Safety is paramount in warehouse operations, and the design of the racking system must prioritize the well-being of employees, the security of inventory, and the overall warehouse environment.
During the design period of the warehouse racking layout, you must ensure that racks are designed and labeled with their load capacity clearly indicated. And during operations, it is your responsibility to train employees to adhere to weight limits to prevent accidents and structural damage.
As precautions, you can incorporate safety features like guardrails, bollards, and safety nets to prevent accidental falls and collisions with racks. It is also important to provide adequate lighting within the warehouse since it ensures a safe working environment and helps prevent accidents related to low visibility.
9. Material Handling Equipment
Selecting the appropriate material handling equipment is a pivotal aspect of warehouse racking system design. The chosen equipment must align with the overall layout and storage configuration. Forklifts, a common workhorse in warehouses, need compatible racking systems that can handle their weight and reach. Similarly, reach trucks and order pickers are most efficient with racking layouts that allow vertical storage and smooth maneuvering.
To put it simply, it is important to coordinate material handling equipment with the type of racking system they work best with for proper inventory retrieval and care.
10. Cost Analysis And Budget Considerations
Careful cost analysis and budget considerations are fundamental during the design phase of a warehouse racking system. It’s crucial to strike a balance between efficiency and cost-effectiveness. Calculating the Total Cost of Ownership is key to achieving a great layout within your budget.
A thorough cost-benefit analysis also aids in comparing various racking options, assisting in the selection of a system that provides optimal value and aligns with the organization’s financial objectives. It will also help determine future maintenance expenses and budget for potential expansions.
Bottom Line
In the dynamic world of warehousing, the design of a racking system is more than just arranging shelves—it’s an art and a science. A well-optimized warehouse racking layout is the backbone of an efficient operation, impacting everything from inventory management to traffic flow. Knowing the factors to consider while designing pallet racks and their layout is essential to achieving a productive, safe, and efficient warehouse.
To help you through this process, our team at Midwest Distribution LLC is here with adequate solutions for all types of warehouses. Remember, a thoughtfully designed racking system isn’t just a storage solution; it’s a strategic advantage that propels your business forward. And we are pros at that!