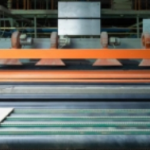
8 Benefits of Choosing Laser Cutting for Metal Sheet Fabrication Projects
July 21, 2023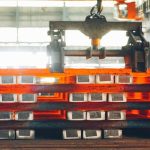
Galvanizing metal- Everything you need to know
August 18, 2023Implementing the right rack system in a warehouse can help optimize its storage space and improve order fulfilment efficiency. However, this task can quickly get overwhelming since dozens of options are available. To help you select the perfect one for your space and business needs, let’s look more closely at some of the different warehouse rack types commonly used in warehouses today.
Warehouse Rack Types That Increase Storage Efficiency
1. Pallet Racking
Pallet racking is one of the most commonly used warehouse storage solutions across the globe. As the name suggests, it is designed to store merchandise packed in pallets that can be accessed with forklifts.
This versatile racking warehouse system consists of uprights, beams, and shelving materials. It helps increase a facility’s storage capacity by optimizing the space.
There are several variations of pallet racking systems, such as selective, double deep, drive-in, drive-thru, etc. We’ll take a closer look at each one.
2. Selective Pallet Racking
This type of pallet racking system is designed to store only one pallet deep. Forklifts can immediately access every pallet. So selective pallet racking is the ideal solution for warehouses that store perishable products or have low volumes of a lot of different products.
The racks are usually installed back-to-back. This helps maximize the storage capacity of the facility by reducing the amount of space used by aisles.
3. Double Deep Pallet Racking
Double deep warehouse rack systems are a lot like selective racks. The only difference is that pallets are stored up to two deep on the bay.
This small change helps improve the warehouse’s storage efficiency. It facilitates the bulk storage of the same product and decreases the total amount of aisles needed in the facility. However, since pallets are stored two deep, you will need forklifts with longer tynes to reach the second pallet.
4. Pushback Racking System
A pushback racking system is a warehouse storage solution that allows multiple pallets of the same product to be stored in the same place, up to six pallets deep. So this high-density racking system can significantly increase storage efficiency. Moreover, it helps minimize the floor space used by aisles between the racking frames.
Forklifts can load and remove pallets from the front. Since the racks are assembled at a slight incline, pallets slide forward when one is picked from the rack. For this reason, it is suitable for FILO (first-in, last-out) product rotation.
5. Carton Flow Rack Systems
A carton flow rack system is a storage solution for small products that are not heavy or bulky. In fact, it’s best suited for cartons that do not require additional handling or elevation equipment. However, it can also be used in combination with other racking solutions, such as pallet racking systems.
Carton flow rack systems consist of sloping roller tracks arranged on different levels to help create different storage lanes. Since the pulley rails are on a slight incline, gravity helps the goods slide down. The slope and the distance between pulley rails can be easily modified to cater to different sizes and shapes.
In addition to this, they have one dedicated loading end and one retrieval end. So it helps support a FIFO (first-in-first-out) inventory management system. That means the stock is consistently rotated, ensuring older stock is picked first.
6. Cantilever Racks
Cantilever racking systems are designed to help store long, bulky items horizontally, such as lumber, pipes, tubes, steel bars, etc. Unlike other racking systems, this storage solution does not have horizontal shelves or upright beams. Instead, it consists of posts with large protruding arms that are bolted at the base.
Since there is no interference from other racking or shelving components, goods can be easily stored and accessed manually or with a forklift. Moreover, the minimalist design reduces wasted storage space.
7. Drive-In Racking System
A drive-in racking system allows forklifts to drive into and back out of a rack from the same end. Since forklifts enter and exit the racking system from the same place, this storage solution is suitable for a LIFO inventory management system.
Drive-in racking systems are designed to store merchandise several pallets deep, making it an ideal storage solution for companies that need to store large quantities of the same product. Moreover, drive-in racking systems help optimize floor space by eliminating the need for picking aisles between the racking frames. That’s why many opt for these high-density, space-efficient racks in warehouses.
8. Drive-Thru Racking
Drive-thru racking systems are slightly different from drive-in racks. In this racking solution, forklifts can enter from both ends of the racking structure – one is used for unloading, while the other is used only for loading. So yes, FIFO inventory management is used, enabling warehouse owners to store items that need to be rotated quickly, such as perishable products.
9. Mobile Racking System
Mobile racking systems utilize rows of mobile shelving that move on trackways built into the warehouse floor. The system has electric motors that allow the racks to move from one side to the other.
Mobile racking systems can help increase the storage capacity of a facility since it eliminates the need for picking aisles between fixed racks. However, it is more suitable for slow-moving inventory.
10. Automated Storage and Retrieval Systems (AS/RS)
AS/RS are advanced, automated warehouse racking systems that utilize the latest tech, such as robots and computerized controls to deposit and retrieve merchandise automatically. AS/RS help manage inventory with accuracy and speed, as well as reduce labor costs. So this warehouse racking solution is ideal for companies that store high volumes of fast-moving stock.
Over to You
Well-designed, advanced material racking systems create the framework for successful storage facilities. They can help increase efficiency, streamline workflows, and improve storage capacity. Needless to say, the right racking system in your warehouse can help make your company more profitable.
If you need assistance choosing a racking solution, Midwest Distribution can help. We have years of experience in creating customized racking systems. So we can design one that utilizes your space by maximizing density and optimizing efficiency. More importantly, our solutions are built to last. Partnering with us means you’re making a wise, long-term investment for the betterment of your company.
Contact one of our representatives to discuss what warehouse rack types are suitable for your business and to get more information about how to enhance the storage efficiency of your facility.