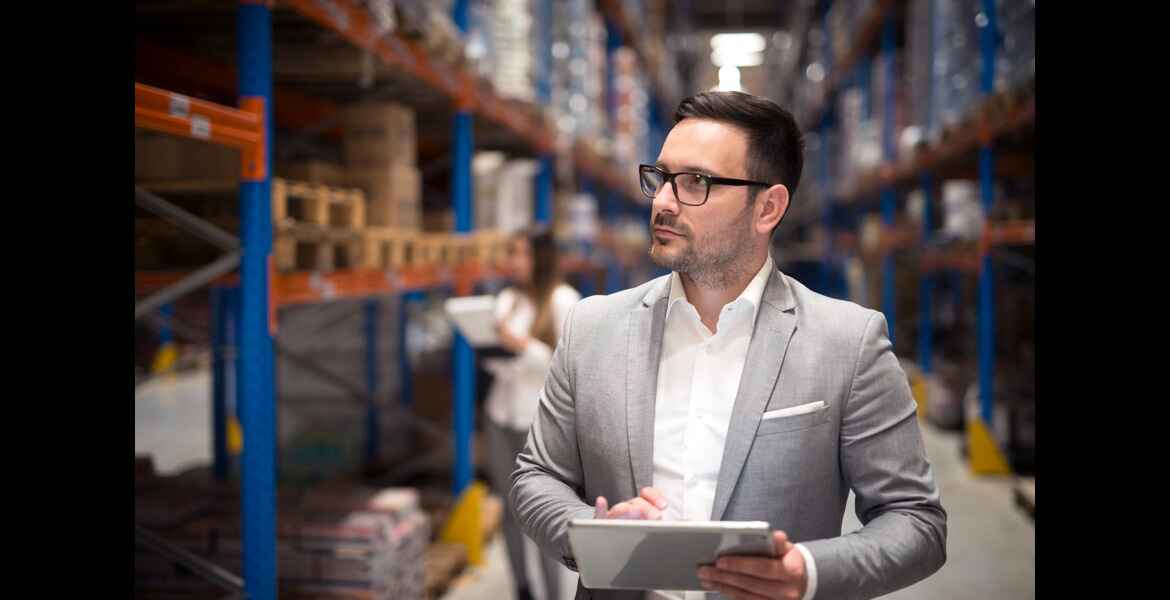
How to Optimize Warehouse Storage- A Complete Guide
Storage optimization is critical for enhancing storage capacity and operational efficiency inside warehouses. It prevents organizations from encountering consequences like lost stocks, blocked aisles, and poor productivity. Eventually, warehouse storage optimization becomes critical for better business and return on investment.
Warehouse managers sometimes need help with stock storage and might be tempted to purchase a bigger unit. However, considering the monetary and operational constraints, that’s not always a viable solution. So, they often have limited space to adjust and manage stocks.
But how can store managers optimize their warehouses for more storage capacity and fluency of operations? In this post, we will look at some valuable tips that can enhance your warehouse storage and help you streamline warehouse operations, providing better efficiency in your daily workflows.
The Outcomes of Warehouse Storage Optimization
Warehouse optimization refers to improving access to stored products and creating more room inside the warehouse. Typically, warehouse managers can experience obstacles and need more storage due to seasonal sales, low sales, or a quickly growing inventory.
So, to make room for more products, it’s essential that warehouse managers allocate adequate space for storage and operations inside the facility. Therefore, the primary objectives behind warehouse storage optimization are to:
- Make warehouse products more accessible.
- Improve mobility inside the warehouse.
- Create more space to accommodate incoming items.
Best Practices to Optimize Warehouse Storage
Warehouse storage optimization starts with a simplified approach for calculating the available space, eliminating unnecessary free space, and using the right tools to implement and monitor the optimization. If you’re a warehouse manager, here is how to start storage optimization for your warehouse.
1. Understand Your Current Space Usage
It all starts with evaluating your current use of space. This step should highlight how much space is used and for what purposes. While analyzing your storage space, you can start with these basic calculations such as:
- Calculating the usable warehouse space = the total warehouse size volume minus the volume of the unused spaces inside the warehouse. This will provide you with the potential space where you can store your warehouse products depending on their shape and size.
- Potential Storage Space – It’s a percentage of your storage size to the total warehouse size. It allows you to determine the potential storage capacity that may be currently unused. Typically, the potential storage space is around 22 to 27 percent. However, anything below 22 percent means you can optimize for more storage.
- Space Utilization – It’s the total volume of the stored units and items inside the warehouse. Generally, this information is available in warehouse management software that is operational inside your warehouse.
2. Get More Space with Better Beam Placement
Placing your rack beams strategically can give you additional space inside the warehouse. For instance, there is a six-inch room between the product’s top and the beam rack’s bottom to accommodate forklift interaction. So, you can optimize the beam height if there is a larger space than needed.
For this purpose, you must measure the height from the top of the product and the remaining space between the rack beams. You can optimize the space by adjusting the beam height if you have more space. However, it also depends on whether you will store the same products every time or whether something taller might be stored there in the future.
3. Use the Right Containers
Typically, warehouses use a standard container to store all the unpackaged goods. These containers are often too large for the products inside them. Hence, picking the right-sized containers can save more space on the shelves.
It’s a good idea to have a rack with varying container sizes. Each container stores the products that fit best. That way, you can remove unneeded containers from the shelves to maximize rack space and store more products.
For this purpose, you can:
- Sort your unpackaged products by size.
- Store products in appropriate-size containers.
- Store the unused containers in one section of the warehouse.
Picking the proper containers will yield extra storage space and help optimize the space better.
4. Get Rid of Obsolete Inventory
Almost every warehouse has unused or unsold inventory. Therefore, eliminating such inventory is a good option for optimizing warehouse storage. This is where an inventory management system becomes so critical.
Hence, you should start by analyzing your inventory findings to locate obsolete products. Make a list of unpacked items and make a strategy to sell them in bulk. You might need to contact the sales team to decide on discount prices and possible charity options for these products.
The idea is to free up space in the warehouse, so anything that removes the unpacked items should be good enough.
5. Store Your Items Based on their Sizes
Storing similarly-sized products can help optimize warehouse storage. This way, sort your products according to size and fix a size range for each warehouse section. You can adjust more products on a single pallet, which might otherwise be unused.
Size-based sorting can also optimize product access, helping the operators to retrieve products quicker. On top of that, it maximizes storage and reduces the chances of product misplacement.
6. Use Vertical Space
Putting vertical space to use is one of the most effective ways to optimize your warehouse storage. For that, determine the distance between the floor and the roof to calculate the possibility of multiple racking.
Next, figure out which inventory can be placed vertically. Vertical space usage increases your storage space. It helps make way for forklifts and optimizes aisle space. Hence, it’s a cost-effective option for storage managers.
7. Clean Up the Floor
The floors of warehouse storage facilities tend to get messy and cluttered. But regular cleaning and clearing away stockpiles from the aisles can allow you to use the floor space better – and keep the facility safe.
So the simplest way you can optimize your floor space is to reserve it only for active inventory. That means relocating unused equipment and pallets that could be taking up your valuable floor space to other locations of the facility. Your goal should be to prevent things from accumulating in places reserved for inventory and stock.
Over to You
Optimization is critical for effective warehousing and storage. It ensures you can use the space for the proper operations and reduce overhead costs on extra space acquisition. Using the appropriate warehouse management system that suits your operations is also a good idea.
Moreover, it’s better to seek professional help for warehouse storage optimization. Companies like Midwest Distribution provide tailored storage solutions for your warehouse to ensure you use the space optimally. So get in touch and organize your warehouse right away.
Sorry, the comment form is closed at this time.